What is Plastic Injection Molding?
Injection molding is the most cost-effective method for mass-producing plastic components. The process involves injecting molten plastic into a mold and then ejecting the solidified part. Since the same mold tool is used for each part, injection molding ensures consistent quality in every piece. Compared to CNC machining or even 3D printing, injection molding offers the widest range of materials, colors, cosmetics, polishing, and surface textures.
YJC's custom plastic molding service provides on-demand prototyping and production molding solutions. We take a customer-centric approach, which means we manufacture parts in the way you need them, without compromising on design, all at an appropriate price. We offer expert consultations for each injection mold quote and assign project managers to every order, ensuring your parts move seamlessly from design to production. Our team has extensive experience across various industries, particularly in medical injection molding and liquid silicone rubber molding.
Our team has experience in every industry, especially medical injection molding ,plastic and liquid silicone rubber(LSR) overmolding.
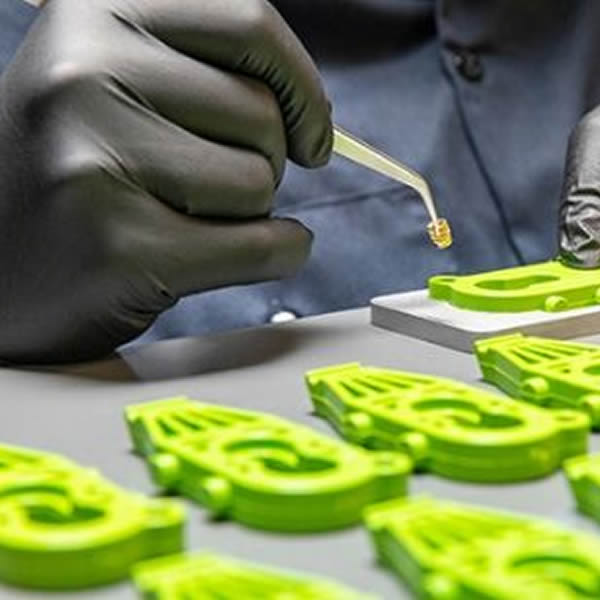
Our Custom Injection Molding Service
Plastic injection molding: Injection molding is a high-pressure manufacturing process that involves injecting thermoplastic materials into a mold. It is the ideal choice for high-volume production, offering cost-effective and efficient manufacturing solutions.
Choose YJC for Parts of Any Complexity, Ranging from 3 mm to 1 m in Size. Experience industry-leading lead times as fast as 20 days. Our extensive manufacturing employs injection machines ranging from 60 to 1300 tons, catering to various part sizes, complexities, and volumes. For precision requirements, tighter tolerances are available upon request. Partner with us for top-quality parts delivered on time and tailored to your specific needs.
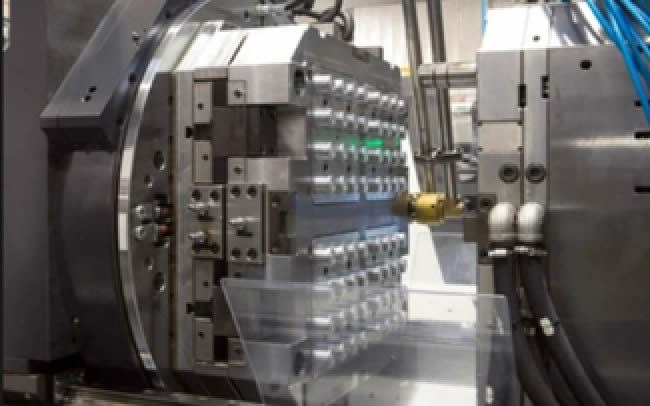
Plastic 2-shot molding
Also Known as two-color or dual-material injection molding, refers to the process of injecting two different materials into the same mold to create a single, integrated part. This manufacturing technique allows for the formation of a molded product using two distinct materials, which can differ in color or hardness, enhancing the product's aesthetics and assembly performance.
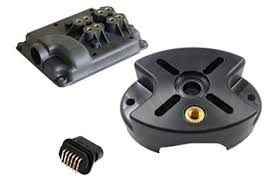
Plastic & metal Insert molding
Insert molding is an injection molding process that works especially well for parts that have threaded holes. It can also help you create better wheels, pulleys, fan blades, and other similar parts.
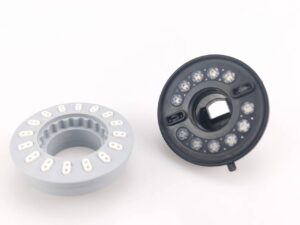
Plastic & LSR Over-molding
Plastic and LSR (Liquid Silicone Rubber) over-molding is an innovative manufacturing process that combines the advantages of both plastic and silicone materials to create high-performance, multi-material parts. In this process, a plastic substrate is first injection-molded, and then a layer of LSR is applied over specific areas of the plastic part.
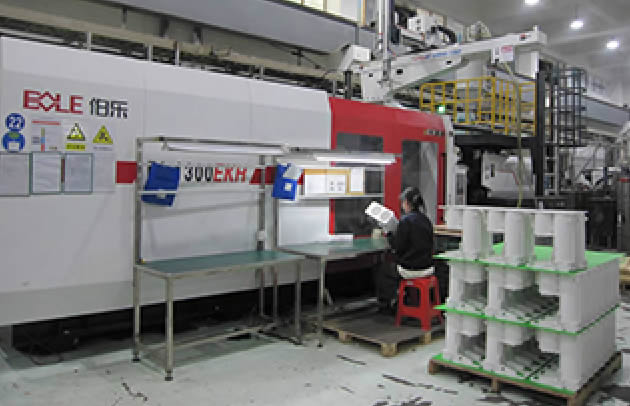
Large Part Injection Molding
Large part injection molding is a specialized manufacturing process used to produce oversized plastic components and parts. This technique is particularly suitable for creating large and complex parts that are difficult or impossible to produce using traditional molding methods
Advantages of Plastic Injection Molding Technology
High Precision and Complex Geometries: Through precise mold design and advanced injection molding techniques, we can produce plastic parts with high precision and intricate geometries. Whether you require fine details or complex structures, we can meet your requirements.
Mass Production and High Efficiency: Plastic injection molding allows for the simultaneous production of multiple identical or different parts, increasing production efficiency. Our advanced equipment and automated processes reduce production cycles and minimize manual intervention, resulting in cost-effective manufacturing.
Material Diversity and Customization: We offer a wide range of plastic materials to meet the requirements of various industries and applications. Depending on your project needs, we can select suitable materials and accommodate color adjustments, surface treatments, and special requirements.
High Quality and Reliability: We prioritize quality control and process monitoring to ensure that the produced plastic parts meet stringent quality standards. By utilizing plastic injection molding, we provide consistent, dimensionally accurate, and reliable parts.
Our Capabilities for Plastic Injection Molding
Service | Details |
Lead Time | Our services offer fast quote responses with design-for-manufacturing (DFM) feedback within 5 business days. |
Production Options | Domestic and international |
Machines Available | We provide a wide range of molding options, including single, multi-cavity, and family molds, with press tonnage capabilities ranging from 60 to 1,300+ tons. |
Inspection and Certification Options | Includes FAI, FMEA, and PPAP. ISO 9001,, ISO 16949, UL, Class 8 Medical Clean Room molding. |
Tool Ownership | Customer-owned with mold maintenance |
Mold Cavity Tolerances | a tolerance of +/- 0.005mm during mold machining while considering the shrink rate. |
Part to Part Repeatability | +/- 0.01mm or less |
Critical Feature Tolerances | YJC Polymer ensures critical features are milled to a steel-safe condition for optimal precision.. |
Available Mold Types | Single-Cavity Molds, Multi-Cavity Molds, Family Molds, and the production cycles will be under 1000 cycles, under 100,000 cycles, under 500,000 cycles and over 1000,000 cycles |
Secondary Operations
We provide various secondary operations, including painting and heat-tapping inserts, among others. For your specific needs, please mention the required secondary operations in the "custom requirements" section of your quote request.
Design Guidelines for Custom Injection Moldings
Feature | Tip |
Undercuts | Incorporating pass-thru coring helps to minimize undercuts, thereby reducing the complexity and cost of the tool's ejection mechanisms. |
Wall Thickness | Maintaining uniform wall thickness in plastic parts helps prevent wall sink and voids, while thinner walls contribute to shorter cycle times and lower manufacturing costs. |
Drafts | Ensure parts are designed with a minimum draft angle of 0.3°, or up to 5°, for faces with medium textures. |
Ribs/Gussets | Ribs should be 40-60% the thickness of outer walls and should still maintain draft. |
Bosses | To ensure structural integrity, bosses should be designed at 30% of the wall thickness in depth, featuring a 30% edge groove, and attached to side walls or ribs. |
How We Manage Your Injection Molding Project
Step | Description |
Upload Design | Submit your product's 3D design for review by our specialist team. Receive expert insights and recommendations. |
Receive Quote | Collaborate with your account manager and technical team to get a detailed quote within 48 hours. |
DFM & Tool Approval | Review the Design For Manufacturing (DFM) analysis for your approval before tool construction begins. |
Receive T1 Samples | Prior to production, receive a golden sample for approval to ensure it meets your specifications. |
Production & Delivery | Parts are manufactured to match the approved sample and promptly delivered to your location. |
Reorder as Required | Easily reorder parts by contacting your account manager for any future requirements. |
Surface Finish Options
Draft angle requirements will vary by requested finish. Industry standard Mold-Tech finishes are also available.
FINISH | DESCRIPTION |
PM-F0 | non-cosmetic, finish to Protolabs' discretion |
PM-F1 | low-cosmetic, most toolmarks removed |
PM-F2 | non-cosmetic, EDM permissible |
SPI-C1 | 600 grit stone, 10-12 Ra |
PM-T1 | SPI-C1 + light bead blast |
PM-T2 | SPI-C1 + medium bead blast |
SPI-B1 | 600 grit paper, 2-3 Ra |
SPI-A2 | grade #2 diamond buff, 1-2 Ra |
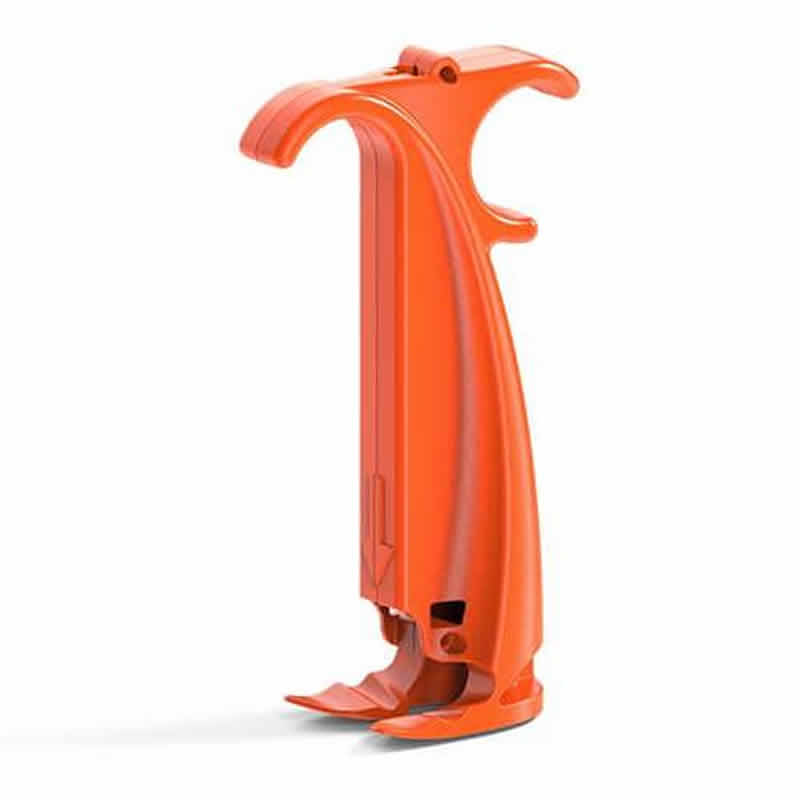
Material & Tolerance
Material
Injection molding uses a huge range of plastics because of many applications across nearly every industry.
Please contact us for specific material requests.
We’ve worked with many types of resins, including:
Property | Materials |
Impact resistant | ABS, PMMA, PVC, PE, PC |
Wear-resistant | POM, PEEK, UHMW |
Dimensional stability | ABS, PBT, HIPS, PPS |
Chemical resistance | PEEK, PP, PBT, PE, LDPE, PA |
Rubber like | TPU, TPE, Silicone |
Cost-efficient | PP, HDPE, LDPE |
Cosmetic | ABS, PC, HIPS |
Tolerance
The specific tolerance range may depending on project requirements, material types, and manufacturing equipment. Here are the typical tolerance range:
Small-sized parts (less than 50 millimeters): it is generally possible to achieve smaller tolerances. Typically, tolerance values range from 0.05 millimeters to 0.2 millimeters.
Medium-sized parts (50 millimeters to 200 millimeters):Generally, tolerance values may range from 0.1 millimeters to 0.5 millimeters.
Large-sized parts (greater than 200 millimeters): the tolerance range may be larger. Generally, tolerance values may range from 0.5 millimeters to 1 millimeter.
Please note that these tolerance ranges are provided as general guidance and may vary depending on project requirements, material characteristics, and manufacturing capabilities. In specific projects, we assess and determine the tolerance range in collaboration with the client, considering their specific needs and design requirements. Need more precise tolerance control? Contact us to discuss and adjust accordingly based on your project requirements. Our goal is to ensure that the produced parts meet design and functional requirements within the tolerance range and provide high-quality finished products.
Applications of Plastic Injection Molding
Plastic injection molding technology finds extensive applications across various industries, including but not limited to:
Automotive Industry: Manufacturing automotive components such as interior parts, exterior components, and functional elements.
Electronics and Electrical: Production of plastic enclosures, connectors, wire harnesses, and other electronic components.
Medical Devices: Manufacturing medical equipment and instruments like syringes, surgical tools, and implants.
Consumer Goods: Production of plastic containers, household items, toys, and more.
Industrial Components: Manufacturing plastic parts for machinery, aerospace, energy, and other industrial sectors.
F.A.Q
Discover how to reduce the manufacturing costs of your custom parts through our injection molding guide, which explores the key factors influencing expenses such as tooling, materials, and production.
Customers own all custom tooling they develop, while reusable proprietary components created by the manufacturing partner (MP) become the MP's property. Custom tooling remains at the MP's facility for a minimum of two years, with the option for extension if needed. Transfers to other locations are possible at the requester's expense.
In the event that an injection molding partner leaves Yjc, we cover the cost of transferring all molds to another manufacturing partner with in our network. This ensures uninterrupted production and timely delivery of your parts.
Upon receiving the order, our manufacturing engineers review the statement of work. A case manager is assigned, and a suitable manufacturing supplier is selected. We create a thorough DFM report for approval. After approval, tooling and mold production begin. T1 samples are produced and sent for approval. Upon approval, the rest of the parts are manufactured.
Having both ISO 9001 and IATF 16949 certifications showcases our dedication to maintaining rigorous quality management practices and meeting the stringent requirements of our client’s industry.