Our Services Navigation
LSR Injection Molding Advantages
Precision and Detail: LSR injection molding allows for intricate and detailed designs, making it suitable for producing complex parts with tight tolerances.
Biocompatibility: LSR is a biocompatible material, making it safe for use in medical and healthcare applications, such as medical devices and implants.
Temperature Resistance: LSR exhibits excellent temperature resistance, maintaining its properties over a wide range of temperatures.
Chemical Resistance: LSR is highly resistant to chemicals, solvents, and other harsh substances, making it suitable for various industrial applications.
Versatility: LSR can be used for a wide range of products, from consumer goods to automotive components to medical devices.
Low Waste: The injection molding process generates less waste compared to traditional manufacturing methods.
Design Flexibility: Silicone offers the ability to fill part geometries with tighter tolerances than are possible with a thermoplastic elastomer. Precise features, varying wall thickness, reduced likelihood of sink, small undercuts and negative draft are all possible with LSR.
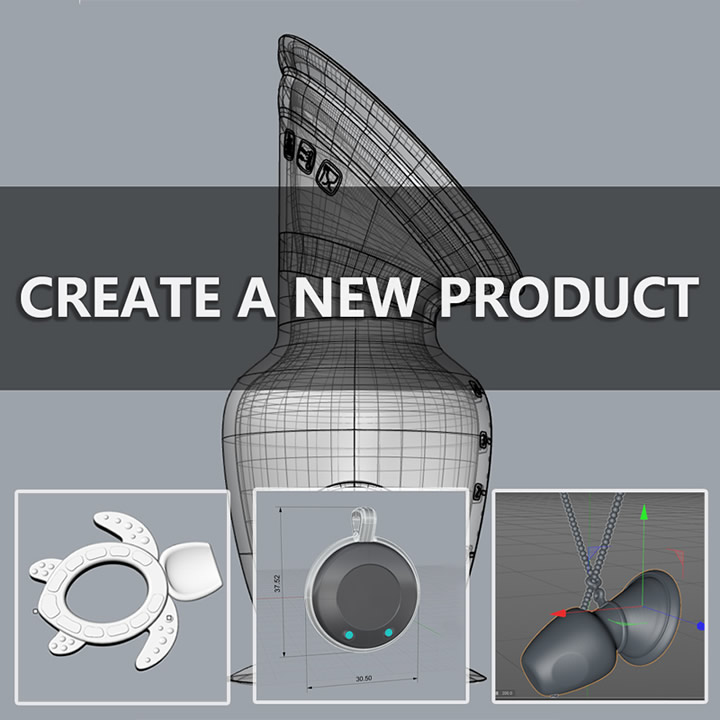
Main Process of Silicone Injection Molding
Raw Material Preparation: First, liquid silicone rubber (LSR) material is mixed with silicone crosslinker and silicone-based fillers to form an LSR compound.
Injection by Injection Molding Machine: The prepared LSR compound is fed into the hopper of the injection molding machine. The machine then heats and injects the LSR compound into the mold cavity.
Mold Filling and Curing: In the mold cavity, the LSR compound quickly fills the entire cavity and then cures due to its inherent heat-reactive properties, forming a solid silicone rubber product.
Cooling and Demolding: After molding, the mold requires cooling to stabilize the silicone rubber. Once cooled, the mold opens, and the solid silicone rubber product is removed, completing the demolding process.
Trimming and Inspection: The extracted silicone rubber product may need trimming to remove excess edges or flash. Then, the finished product undergoes quality inspection to ensure it meets design specifications and quality standards.
Post-processing: For certain applications, post-processing such as surface coating, printing, or bonding may be required.
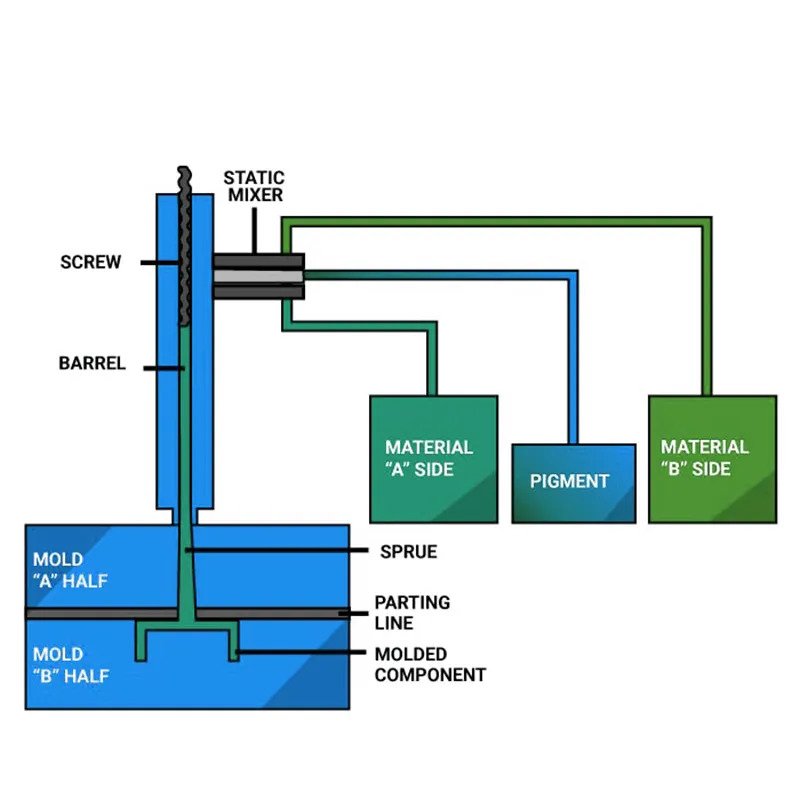
Why Choose Us to Custom Your LSR Molding Service?
15+ Years Silicone Rubber & Plastic Injection Molding Manufacturing Experience
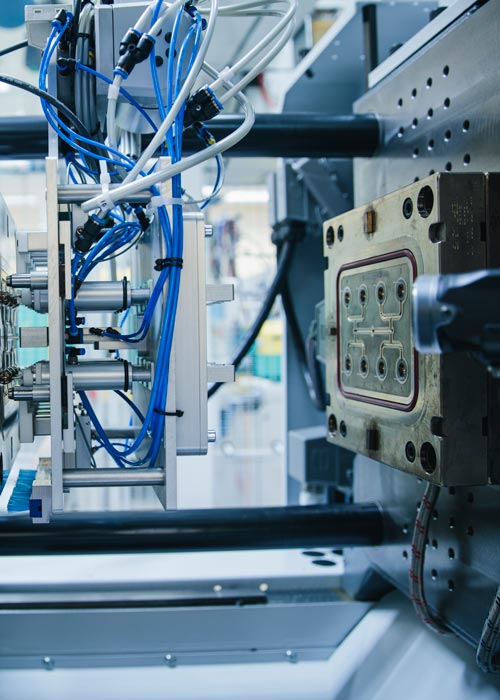
Extensive Production Capacity
YJC offers exciting design and molding opportunities through silicone injection molding. With over 10 sets of LSR injection machines ranging from 60 to 160 tons, our advanced manufacturing facility ensures extensive production capacity and flexibility. Supported by advanced control technology, we deliver high-quality LSR products promptly and provide customized solutions tailored to our customers' specific needs.
Biocompatibility&Performance Properties
We meticulously select and test LSR materials to meet strict medical and healthcare biocompatibility standards for components intended for human contact. Our production process takes place in an advanced 8-grade cleaning room, ensuring a controlled and sterile environment for manufacturing medical-grade LSR components. Adhering to international standards like ISO 9001, our LSR components are safe for medical applications, meeting the stringent requirements of the medical industry.
Multi-material Molding
We excels in multi-material molding, incorporating two-shot, insert, and overmolding techniques. With this advantage, we can combine different LSR materials with other materials in a single mold, allowing for diverse and complex product designs. This flexibility enables us to meet various performance requirements, customize colors, simplify manufacturing processes, and enhance product quality, positioning us as a leading provider in the LSR injection molding industry.
Precise Control
By using high-precision injection molding machines and advanced control systems, we can monitor and adjust key parameters like temperature, pressure, and speed in real-time, ensuring stable and consistent LSR injection. This precise control guarantees consistent product dimensions and quality, meeting the stringent demands for high-quality LSR products from our customers. Whether it's small-batch or large-scale production, we maintain a high level of accuracy throughout the manufacturing process.
Our Silicone Injection Molding Special Capabilities
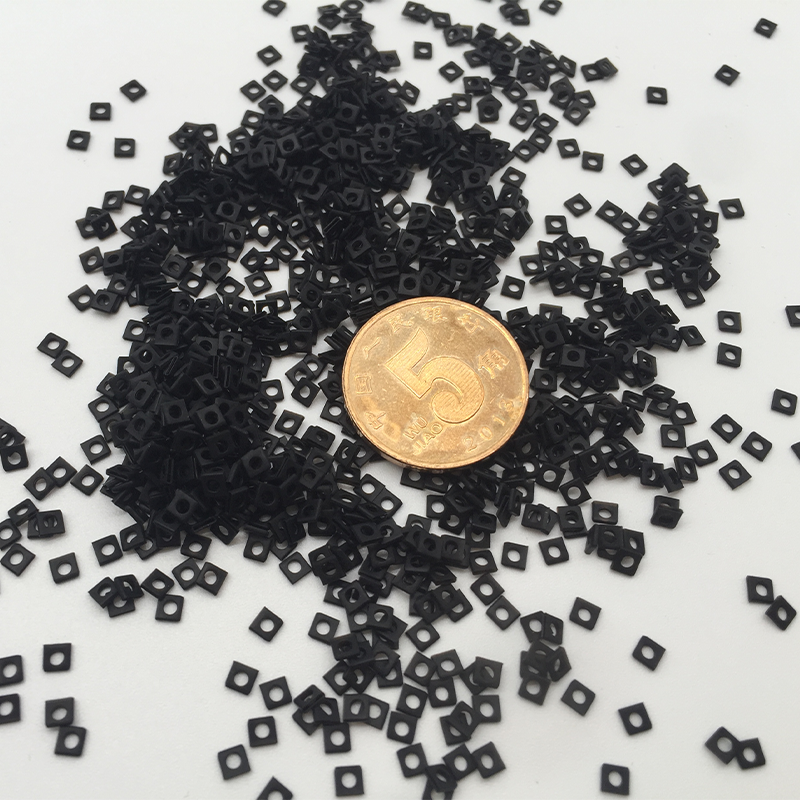
Micro & Nano Technology
Components below 10 milligrams in weight
Flashless production possible with needlepoint injection technology and fully automated parts handling
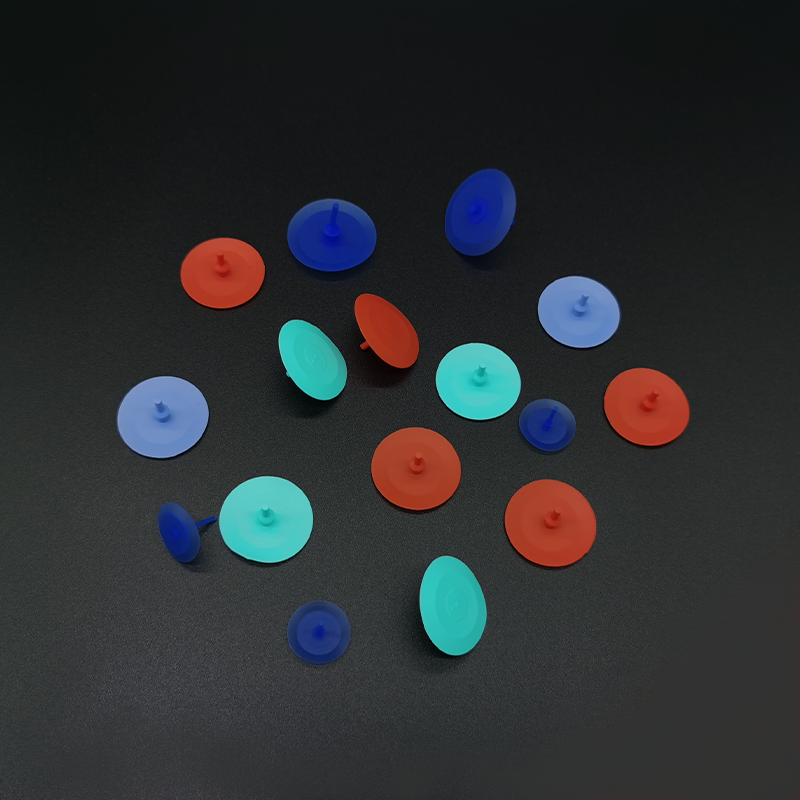
Thin Sections
10mm (0.004 inch) or less
Ideal for thin membranes
Perfect consistency in thickness and quality
No pin holes
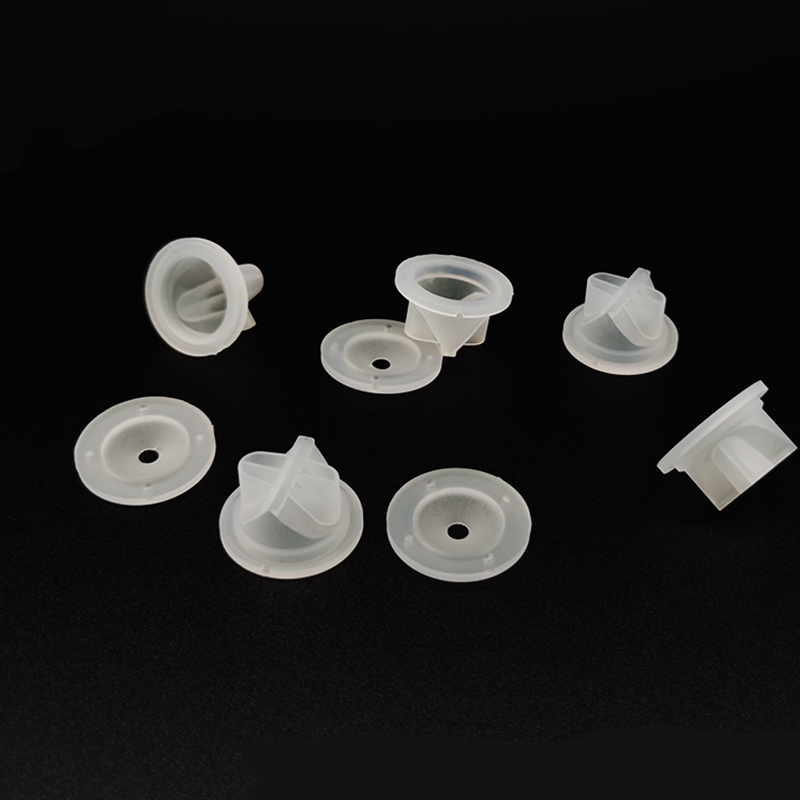
Delicate Parts
Formed reliably every time
Flashless production possible with special tool construction and automation
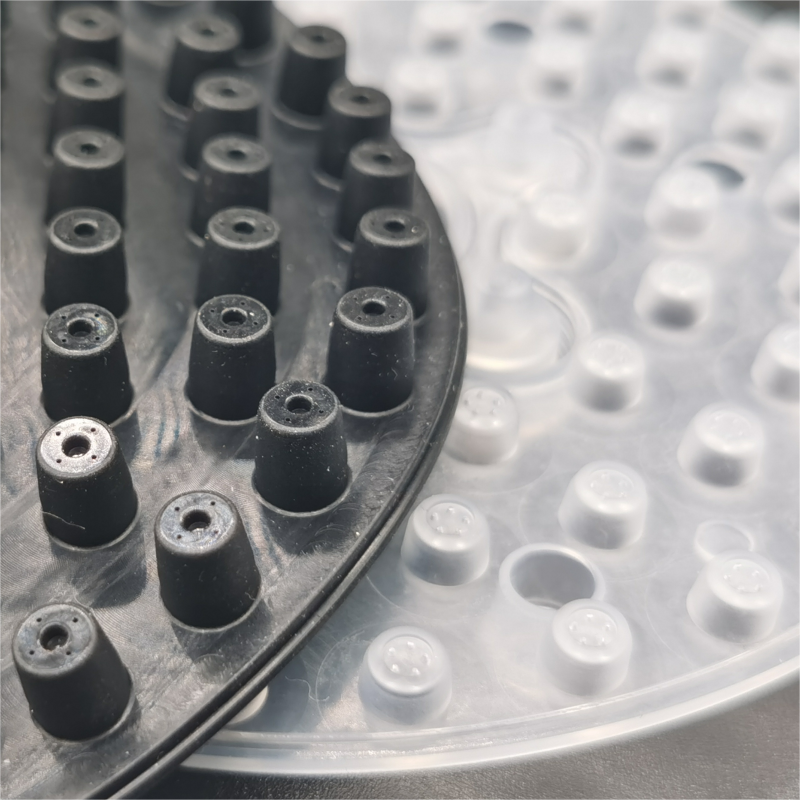
Virtually Flash-Free
No need for secondary deflashing
High dimensional stability directly from mold
Flashless, wasteless design principles
Highest efficiency
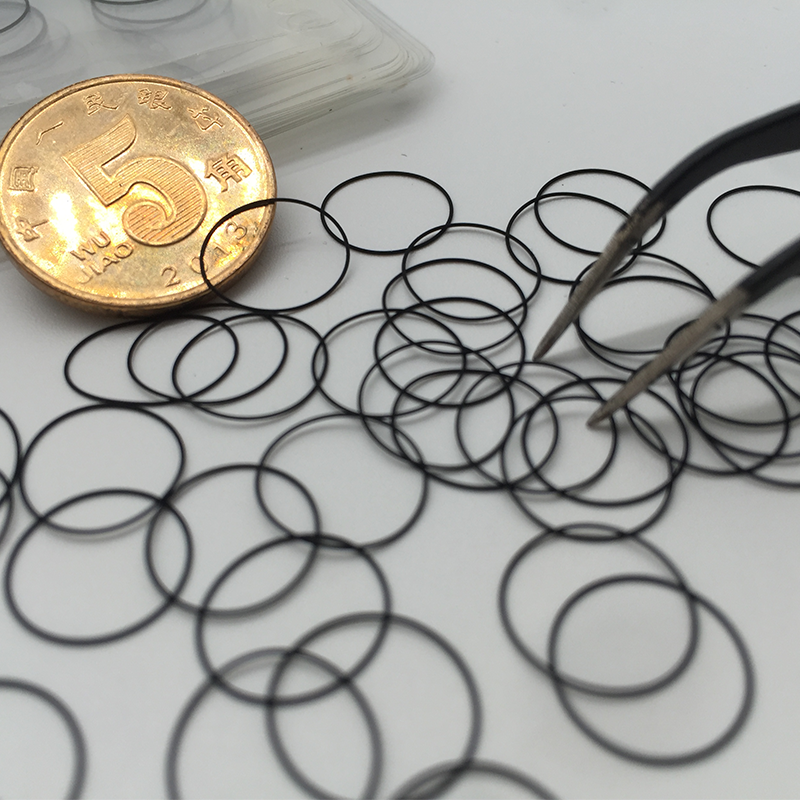
Highest Precision
Surfaces from high polish to
textured
Consistent manufacturing
over millions
of parts
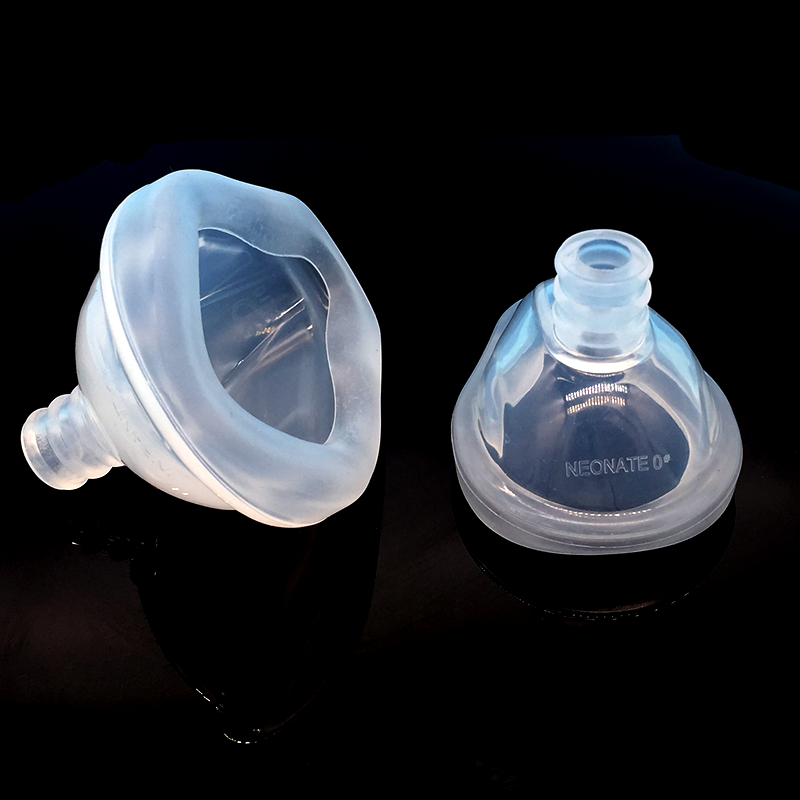
Under Cuts
Common feature in e.g. bellows
Made possible with LSR and special tool construction
for molding
and de-molding
Related Custom Technology of LSR Injection Molding
As a leading provider of LSR injection molding services, we are committed to delivering high-quality solutions. YJC Polymer Co,.Ltd has an ISO class 8 cleaning room with both single-shot and more than 12 sets LSR molding machines, where we also perform post-molding value-added processes. Our professional services include:
Mold Design and Manufacturing
Injection Molding
The most common production process involving the heating and injection of liquid silicone rubber material into mold cavities using injection molding machines, followed by curing into solid silicone rubber products.
Two-Shot Injection Molding
Insert Molding
Overmolding
Involves injecting LSR material into existing part cavities, covering or encapsulating the original part with LSR material to create composite products.
Coating Molding
A process where LSR material is applied as a coating on existing substrates, enhancing or providing specialized properties to the base material.
Cast Molding
Hygienic Molding
LSR parts are produced in a clean, hygienic environment with highly-controlled conditions, such as white rooms or more stringent ISO cleanrooms with various classifications.
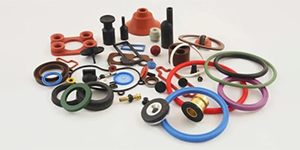
Automotive Industry
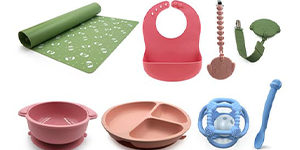
Baby Care
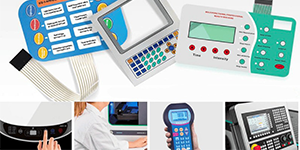
Consumer Electronic
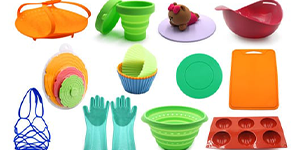
Houseware
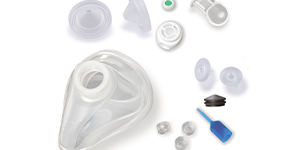
Medical
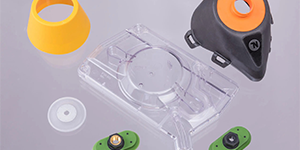
Safety & Specialty
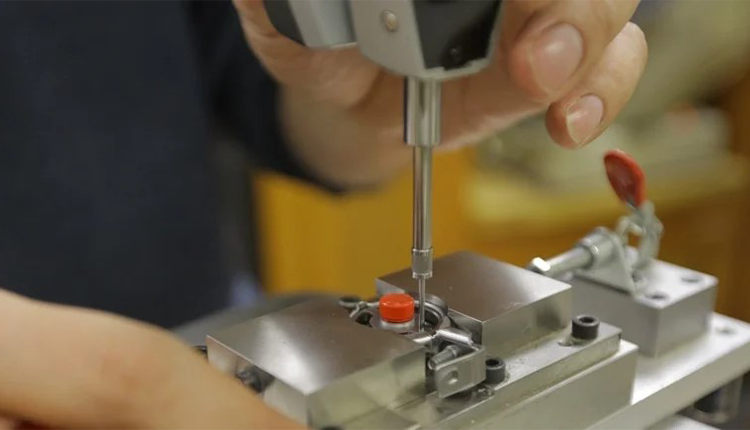
Quality Inspections
Depending on your application's requirements, you can choose from the following when requesting a quote for your silicone rubber parts.
Quality Inspections available for on-demand manufacturing orders
Applications of LSR(Liquid Silicone Rubber) Injection Molding
LSR injection molding technology finds extensive applications across various industries, including but not limited to:
Medical Devices: Manufacturing medical silicone seals, tubes, artificial organs, and more.
Automotive Industry: Producing automotive seals, sound-dampening materials, cushioning pads, and more.
Electronics and Electrical: Creating electronic seals, electrical insulation components, conductive parts, and more.
Baby Products: Crafting safe and comfortable nipples, bottles, breastfeeding devices, and more.
Industrial Sector: Utilizing LSR for seals, protective covers, vibration damping pads, and more.