What is Silicone Rubber Extrusion?
Silicone rubber extrusion is a process used to manufacture continuous lengths of silicone rubber profiles or tubing with consistent cross-sectional shapes. It involves forcing a silicone rubber compound through an extrusion die to create products like seals, gaskets, tubes, cords, and profiles for various applications in industries such as automotive, aerospace, electronics, and healthcare.
Silicone extrusions outperform other materials, offering longer lifespan, various colors, and resilience to diverse environmental conditions. We can produce simple or complex cross-sections, even multi-layered products in an ISO 8 cleanroom.
However, silicone extrusions are susceptible to shrinkage during manufacturing, leading to potential product unreliability and tool wastage. At Lingshantech, we have more than 20 years of experience in designing tooling for silicone extrusions, guaranteeing correct tooling design from the start, and we will continue at our expense until we achieve the desired result.
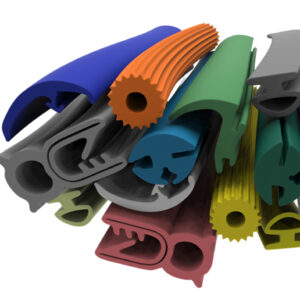
Features
- Flexibility
- Transparency and translucency
- High-temperature resistance
- High resilience and elastic memory
- Biocompatibility
- Chemical resistance
- Processability
- Excellent mechanical properties including tear strength and elongation
- Ceramifiable Flame resistance grade
- Conductive
Our Silicone Material Complies to following:
- FDA Regulation 21CFR177.2600 For Food Contact
- NSF 51 Approved Material
- Chemical Resistance
- 3A Sanitary
- ZZ-R-765 Overtaken by A-A59588
- ASTM D2000, AMS 3304
- USP CL-VI Material
- High Temperature Silicone
- 10 Shore A to 90 Shore A
Custom Silicone and Rubber Extrusion Capabilities
With our extensive experience in producing extruded silicone and rubber products, we possess the expertise to formulate custom compounds that are tailored specifically to meet the unique design and application requirements. This allows us to achieve precise engineered performance while optimizing costs. Our capabilities extend to handling profiles ranging from simple to extraordinarily complex, ensuring that we can fulfill even the most intricate project demands.
Capabilities | Single, co-extrusion, tri-extrusion |
Extrusion process | Multi-lumen, multi-durometer, multi-color, insert |
Cross-section | 0.010” to 3” |
Custom formulations | Mechanical properties, chemical resistance, temperature resistance, electrical properties, thermal properties, color matching |
Value-added services | Die cutting, adhesive application, cutting, bonding, frame and O-ring fabrication, special put-ups, special packaging, PSA application |
Production capabilities | Low to high volumes |
Lead times | Calculated per project |
Advantages of Silicone Rubber Extrusion
The silicone rubber extrusion provides excellent design flexibility, consistency, precision, efficient production capabilities, and exceptional physical properties. It is an ideal choice for manufacturing custom profiles and components in many industries.
Design Flexibility: The extrusion process allows for the creation of complex shapes and profiles. Customized molds and adjustment of extrusion parameters can meet specific design requirements.
Consistency and Precision: Extrusion ensures consistent dimensions and shapes of products. Precise control of extrusion speed and pressure enables highly accurate extruded products.
Efficient Production: Extrusion enables efficient mass production. The continuous extrusion process allows for the rapid production of large quantities of products with excellent repeatability.
Excellent Physical Properties: Silicone and rubber products produced through extrusion exhibit exceptional physical properties such as heat resistance, chemical resistance, aging resistance, and elasticity. This makes them suitable for a wide range of applications.
Material Versatility: The extrusion process accommodates various types of silicone and rubber materials, including silicone rubber, fluorocarbon rubber, nitrile rubber, and more. The selection of the most suitable material can be based on specific performance requirements.
Cost-effectiveness: Extrusion typically offers cost-effective manufacturing. The efficiency of continuous extrusion production and improved material utilization help lower production costs and enhance manufacturing efficiency.
Process of Silicone Rubber Extrusion
Material Selection:Careful selection of the appropriate silicone or rubber material based on the desired properties and application requirements. Factors such as temperature resistance, chemical compatibility, and flexibility are taken into consideration.
Material Preparation:The selected silicone or rubber material is prepared by mixing it with additives and other components to achieve the desired properties and consistency. This mixture is often referred to as a compound.
Extrusion Die Design:The design of the extrusion die is critical to achieving the desired shape and dimensions of the extruded product. The die is custom-made based on the specific requirements of the application.
Extrusion Process:The compound is fed into an extruder, which consists of a screw inside a heated barrel. The screw rotates, forcing the compound through the barrel, melting it and creating pressure.
Die and Cross-Head:The molten compound is pushed through the extrusion die, which gives it the desired shape and size. A cross-head is often used to guide the compound as it enters the die, ensuring uniform flow.
Cooling and Curing:The extruded product is then cooled to solidify and stabilize its shape. Depending on the material, curing may also be required to achieve the desired properties. Heat or other curing methods may be applied.
Cutting and Finishing:Once cooled and cured, the extruded product is cut into the desired lengths or shapes. Additional finishing processes, such as trimming, punching, or surface treatments, may be performed to meet specific requirements.
Quality Control:Throughout the extrusion process, quality control measures are implemented to ensure that the extruded products meet the required specifications. Dimensional checks, visual inspections, and material testing are commonly performed.
Packaging and Delivery:The finished extruded products are carefully packaged to protect them during transportation and storage. They are then delivered to the customers according to their specific requirements and timelines.
By following this comprehensive extrusion process, we can produce high-quality silicone and rubber extruded products that meet the strictest standards and exceed customer expectations. Our expertise and commitment to precision ensure consistent results and customer satisfaction.
YJC Custom Solution of Silicone Rubber Extrusion
Expertise in the Process: With 15 years of experience and specialized knowledge in extrusion manufacturing, our team is well-versed in every aspect of the silicone and rubber extrusion process. From material selection to die design and control of extrusion parameters, we ensure product quality and consistency.
Customization Capability: We have the ability to customize the manufacturing of silicone and rubber extruded components according to specific customer requirements and design needs. Our engineering team works closely with customers, providing technical consultation and design support to ensure the final product meets their expectations.
Material Selection and Formulation Optimization: We offer a wide range of silicone and rubber material choices and can optimize formulations to meet specific physical performance requirements based on customer's application needs. Our team of experts conducts material selection and testing to ensure the performance and reliability of the extruded components.
Manufacturing Precision: By tightly controlling parameters such as temperature, pressure, and speed during the extrusion process, we can produce silicone and rubber extruded components with precise dimensions and consistency. We employ advanced equipment and monitoring systems to ensure product quality and manufacturing precision.
Capability to Handle Complex Shapes: We have the ability to handle a variety of complex shapes, whether it's intricate cross-sectional designs, detailed features, or extruded components with special requirements. Our technical team and process engineers are adept at addressing the challenges posed by complex shapes and ensuring the manufacture of extruded components that meet design specifications.
Quality Control and Certifications: We strictly adhere to quality control standards and processes to ensure that each extruded component meets industry standards and customer requirements. Our manufacturing processes comply with ISO quality management systems, and we can provide relevant certification documents and test reports.
With these advantages, we are able to deliver high-quality, customized extruded silicone and rubber components that meet the needs and challenges of various industries. We are committed to continuous improvement and technological innovation, providing reliable solutions and excellent manufacturing services to our customers.
Common Types of Silicone Rubber Extruded Components
There are various types of extruded silicone and rubber components based on their shapes and applications. Here are some common types of extruded silicone and rubber components:
Seals: Including O-rings, sealing strips, gaskets, etc., used to prevent leakage of liquids or gases.
Gaskets: Used to fill and seal gaps between two or more parts.
Tubing and Fittings: Used in piping systems to convey liquids, gases, or powders, such as hoses, pipe fittings, etc.
Protective Sleeves: Used to protect wires, cables, pipes, or other components from damage or external environmental influences.
Elastic Cushions: Used to provide cushioning, shock absorption, or support, such as shock absorbers, spring mounts, etc.
Angle Bars and Edge Protectors: Used to protect surfaces from scratches, impacts, or other damages, such as angle bars, edge protectors, etc.
Rails and Guides: Used to provide directional guidance and support for motion, such as slides, guide bars, etc.
Screens and Filters: Mesh structures used for separating solid particles or filtering liquids, such as screens, filters, etc.
Fillers and Sealing Elements: Used to fill gaps, voids, or holes to provide sound insulation, thermal insulation, or waterproofing properties.
Custom Extruded Components: Customized extruded components manufactured according to specific customer needs and design requirements, can have various shapes and functionalities.
Applications:
Typical Applications of Extruded Silicone Profiles
Automotive – Seals & Gaskets
Aerospace and military Seals & Gaskets
Meat Processing – Hatch Seal, Chamber Seals
Lighting Industries-
Construction -(door seals, window seals, protective seals between glass & steels)
Dairy Fluid Handling Tubing and Dairy Seals
Electronics washers, spacers and seals
Door Seals & Gaskets
Oven and manway seals
High temperature sealing
HVAC Equipment – wire seals, sealing chambers conditioning
Rail and Mass Transit Seals
Oil & Gas resistant seals
Pharmaceutical USP Class Vi Tubing and Custom Seals
Marine and Defense – Hatch Seal, Inflatable Seals, Molded Rubber Parts