LSR Injection Mold with Cold Runner System
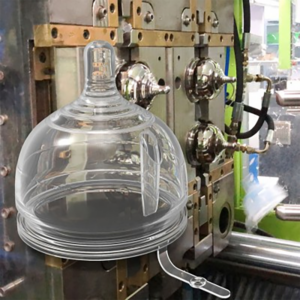
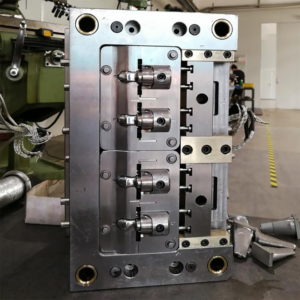
1.Bridge tooling
2.Functional prototyping
3.Low-volume production
4.Production
5.Various stocked liquid silicone,from FDA to medical silicone certified
Overview of Liquid Silicone Injection Molding
LSR Moulding is a manufacturing process that involves injecting liquid silicone into a mold cavity under high pressure.
The LSR injection Molding process is similar to plastic injection molding but uses liquid silicone instead of plastic. The liquid silicone is cured in the mold cavity to produce the final product.
Liquid Silicon Injection Molding has become a popular manufacturing technique in recent years because of its ability to produce high-quality rubber products with tight tolerances and complex geometries.
The process is ideal for producing small to medium-sized parts in large volumes.
There are the following forms during liquid silicone injection mould design:
1) Hot Runner with Edge Gate
It is a waste of materials, simple design, low cost, and mostly used for large products.
2) Cold Runner with Needle Valve
It can realize automation and short cycle.
3) Cold runner without Needle Valve
Due to the high expansion coefficient of LSR, it will expand when heated, but it will shrink slightly when cooled, so the parts can not keep accurate side distance in the mold. Therefore, cold channel processing can be used, LSR should keep low temperature and fluidity, cold channel adopts closed system, in the injection cycle, the closed system uses “sealing needle” or “needle valve” in each channel to control the accurate measurement of LSR material.
Free Engineer Early involvement/Design Support (DFM).
Custom Liquid Silicone Rubber Mold LSR Plastic Injection Molding Design with Cold Runner
Liquid Silicone Rubber Mold Design with Cold Runner
In liquid silicone rubber mold design, there are the following forms:
1) Hot Runner
It is a waste of materials, simple design, low cost, and mostly used for large products.
2) Cold Runner with Needle Valve
It can realize automation and short cycle.
3) Cold runner without needle valve
Due to the high expansion coefficient of LSR, it will expand when heated, but it will shrink slightly when cooled, so the parts can not keep accurate side distance in the mold. Therefore, cold channel processing can be used, LSR should keep low temperature and fluidity, cold channel adopts closed system, in the injection cycle, the closed system uses “sealing needle” or “needle valve” in each channel to control the accurate measurement of LSR material.
LSR Iniection Mold Cold Runner Svstem Main Function
- Save time and material within LSR project.
- Higher-quality liquid silicone part production.
- LSR cold runner mold is beneficial to large volume production.
- Liquid injection mold with cold runner can accelerate production andits mold service time is longer.
LSR and LIM’s Benefits
1.LSR is transparent, durable, and ultraviolet and stain resistant.Compared with common rubber, LSR can withstand extreme high and low temperatures, can used in hot and cold environments.
2.LSR can be molded to varying wall thicknesses, within the same part, enabling ease of manufacturing for complex devices, ideal for intricate designs and close-tolerance parts.
3.LSR is liquid fluid, can molded to different thickness easily, can achieve strict tolerance. It’s a better choice for high precision and difficult structure products.
4.LSR Injection Mold’s designs are simplified, as liquid silicone rubber flows readily into very thin cross section. Liquid Injection Mold’s surfaces do not have to be highly polished.
5.LSR Injection Mold’s cure cycle is shot, as the silicone is fully cured, the product is finished with no or less flashing, which can improve efficiency.